Entre Coalmill Raw Ball Mill

Phone
+86 15538087991


Location
No. 201 Huaxiasanlu road, Pudong, Shanghai, China
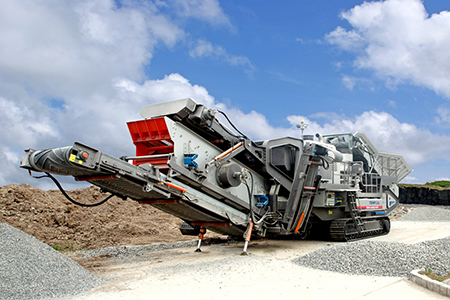
Coal Mill in Cement Plant Vertical Roller Mill Air-Swept Ball Mill
A coal mill is also called a coal pulverizer or coal grinder. It is a mechanical device used to grind raw coal into pulverized coal powders. The most used coal mills in cement plants
More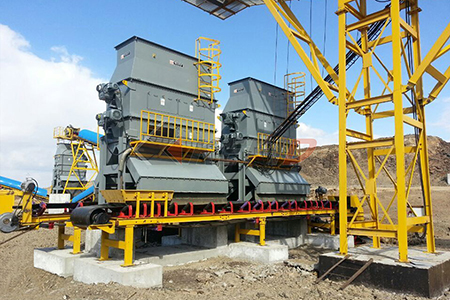
Rawmill - Wikipedia
Wet grinding is more efficient than dry grinding because water coats the newly formed surfaces of broken particles and prevents re-agglomeration. The process of blending and homogenizing the rawmix is also much easier when it is in slurry form. The disadvantage is that the water in the resultant slurry has to be removed subsequently, and this usually requires a lot of energy. While ene
More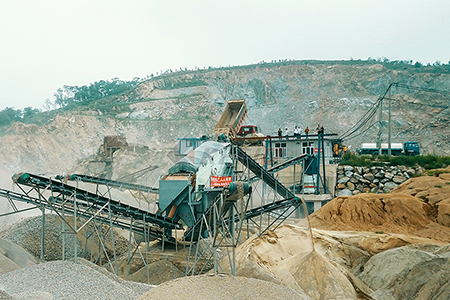
Vertical Roller Mills - FLSmidth
We have supplied vertical roller mills (VRM) for raw, coal, slag and cement grinding for several decades. The vertical roller mill is well known in the cement and power plant
More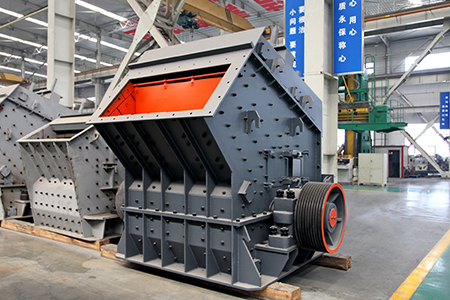
Ball mill - FCB E-mill - Fives - vertical / for coal grinding
Description. Thanks to a bed material grinding concept, the vertical FCB E-mill offers power consumption reduced by 50% compared to the ball mill for coal grinding. Customer benefits Low power consumption Low noise level Low maintenance Constant product quality Technical advantages Long life of grinding balls No sophisticated mechanical ...
More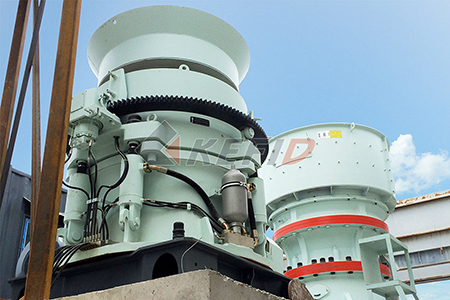
Coal Mill in Cement Plant Vertical Roller Mill Air-Swept Ball Mill
It is a mechanical device used to grind raw coal into pulverized coal powders. The most used coal mills in cement plants are air-swept ball mills and vertical roller mills. At present, most cement plants use coal as the main fuel in the clinker production process. The standard coal consumed by the new dry process for producing 1 ton of cement ...
More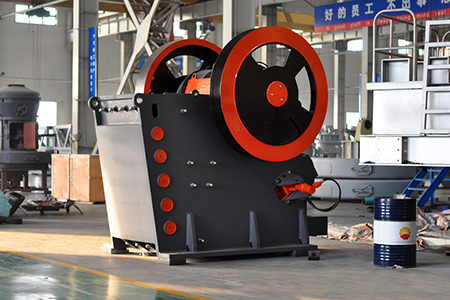
Ventilation Prediction for an Industrial Cement Raw Ball Mill
2021年6月10日 In cement mills, ventilation is a critical key for maintaining temperature and material transportation. However, relationships between operational variables and ventilation factors for an industrial cement ball mill were not addressed until today. This investigation is going to fill this gap based on a newly developed concept named “conscious laboratory
More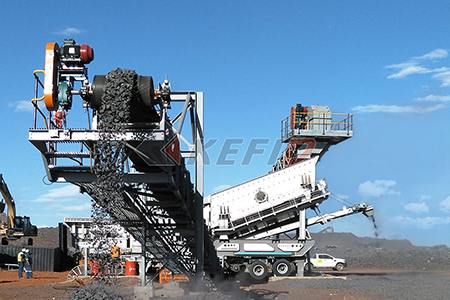
IG PERFORMANCE PARTS Mill Liners for Ball Mills Increase
For a coal mill, we usually recommend a light classifying liners and for raw mills we recommend heavy classifying liners. If the raw materials are particularly coarse, a mixed solution might be best. This could be either by replacing the first few rings – e.g., the first 1.5 m of the chamber – with step lining or combining wave lining
More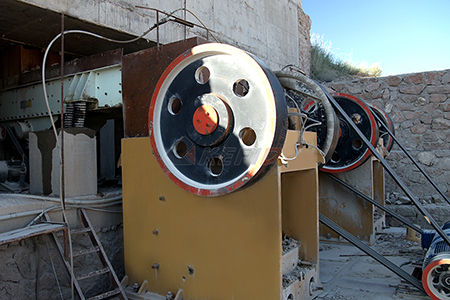
Pulveriser in Thermal Power Plant Bowl Mill Ball Mill
The Ball mill pulveriser is basically horizontal cylindrical tube rotating at low speed on its axis, whose length is slightly more to its diameter. The inside of the Cylinder shell is fitted with heavy cast liners and is filled with cast or forged balls for grinding, to approximately 1/3 of the diameter. Raw coal to be ground is fed from the ...
More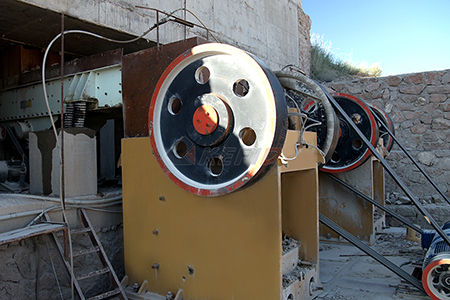
Pulveriser in Thermal Power Plant Bowl Mill Ball Mill
The Ball mill pulveriser is basically horizontal cylindrical tube rotating at low speed on its axis, whose length is slightly more to its diameter. The inside of the Cylinder shell is fitted with heavy cast liners and is filled with cast or forged balls for grinding, to approximately 1/3 of the diameter. Raw coal to be ground is fed from the ...
More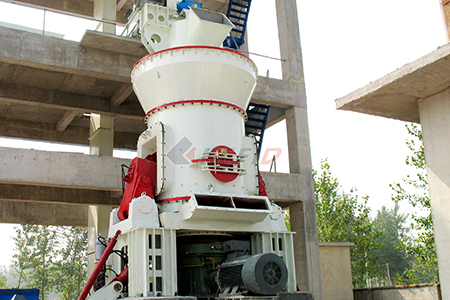
Roller Mill Based on Experimental Method
2022年1月23日 and vertical roller mill i.e., VRM [3–5]. Among these devices, VRM plays an important role in cement, accounting for more than 55% of China’s cement raw meal market [6], and its performance directly affects the cost of producing cement. VRM has the functions of grinding and powder selection, including a grinding unit and an air classifier ...
More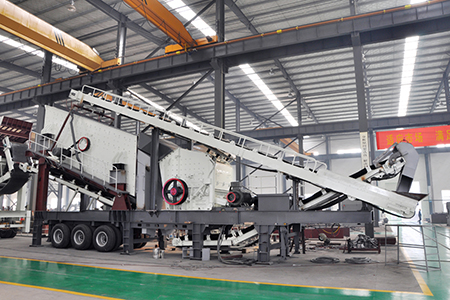
Closed and Open Circuits Ball Mill for Cement, Limestone, Iron ore
It is highly acknowledged for effective and quick grinding in several industries such as limestone, cement, coal, iron ore, chrome ore and many others. The major highlight in the mill is its fully automatic function with PLC control and instrumentation. We are manufacturer and supplier of ball mills since 1980. 400 installations worldwide with ...
More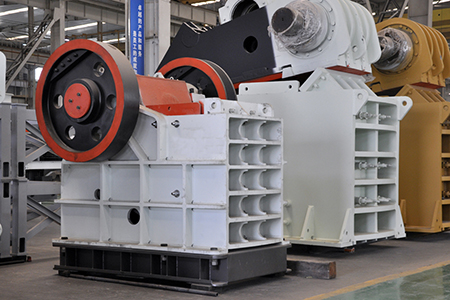
Coal Ball Mill Grinding for Different Kinds of Pulverized Coal
Raw coal enters the coal ball mill through the feeding device. At this time, hot air with a temperature up to 300℃ enters the coal mill barrel from the intake pipe. The raw coal falls on the lifting plate of the drying chamber and is continuously raised. In the process of heat exchange between raw coal and hot air, water is continuously ...
More
Ventilation Prediction for an Industrial Cement Raw Ball Mill by
2021年6月10日 1. Introduction. In the cement industry, grinding is one of the most consuming energy stages in the production units. Around 65% of the total used electrical energy in a cement plant has to be utilized to grind raw materials, coal, and clinker [1,2].Through the process, many variables can affect the efficiency and productivity of
More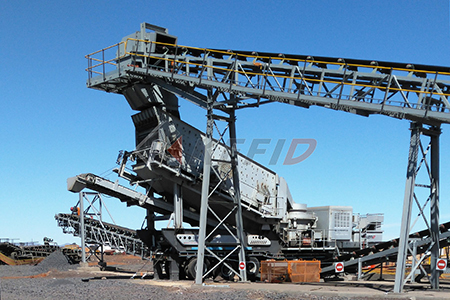
SAG vs. AG Mills: Understanding the Key Differences - ball mills
SAG mills use a combination of steel balls and rock particles as grinding media, while AG mills use only the ore itself. Both types of mills are used for grinding ore in mineral processing operations, but SAG mills are larger in size and can grind larger quantities of ore. AG mills, on the other hand, are smaller and are typically used for ...
More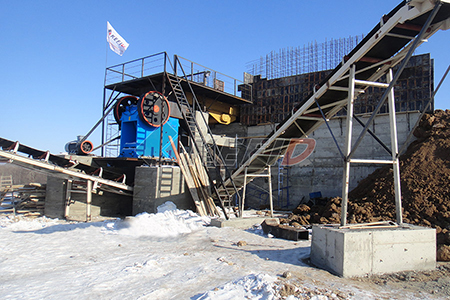
Exploring ball size distribution in coal grinding mills
2014年5月1日 The ball size distribution (BSD) in a mill is usually not known, as the measurement of the charge size distribution requires dumping the load and laboriously grading the balls into size classes. Fortunately we had one set of data as discussed below. The general non-availability of BSD necessitates the use of ball wear theory to estimate
More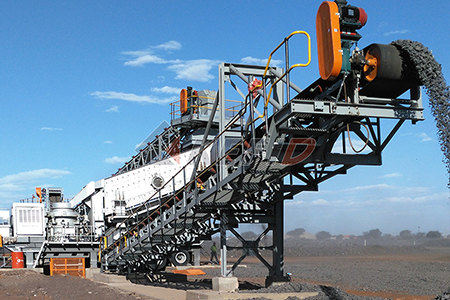
How to choose proper grinding media for your ball
2021年2月24日 Steel balls are one of the most widely used grinding media in cement ball mills, their diameters can range from 20mm to 120mm according to different grinding requirements. In a cement ball mill,
More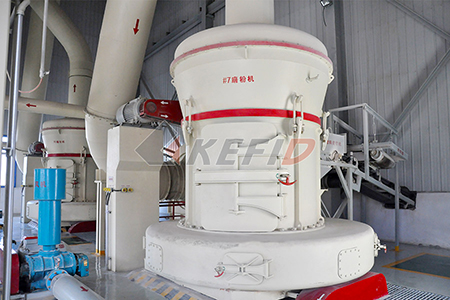
Rawmill - Wikipedia
A raw mill is the equipment used to grind raw materials into "rawmix" during the manufacture of cement. Rawmix is then fed to a cement kiln, which transforms it into clinker, which is then ground to make cement in the cement mill. The raw milling stage of the process effectively defines the chemistry (and therefore physical properties) of the ...
More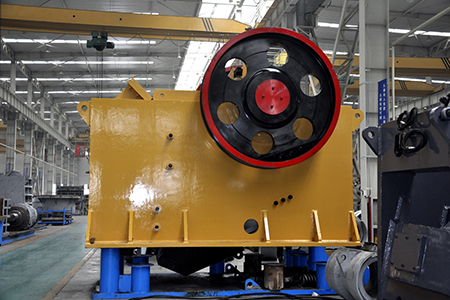
Ball Mill vs Rod Mill: Which is the Best for Your Mining Operation
One of the advantages of a rod mill is that it can handle a higher capacity than a ball mill of the same size. Additionally, the grinding medium in a rod mill is more uniform than that in a ball mill, and this can be beneficial for certain materials. Rod mills are also relatively low-maintenance, making them a cost-effective option for many ...
More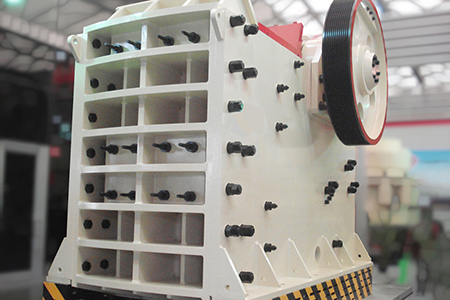
Vertical roller mill for raw Application p rocess materials
are too large to be fed into the tube (ball) mill. (5) Ground materials are dried by the flue gas from the kiln. Fig.2 Schematic process flow of vertical roller mill for grinding of raw materials Vertical roller mills are adopted in 20 cement plants (44 mills) in Japan. Results Table Energy saving effect of the vertical roller mill Ball mill ...
More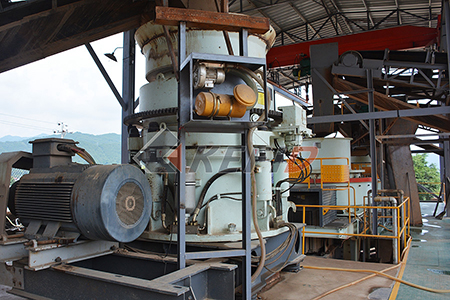
Coal mills for all requirements Gebr. Pfeiffer
Fax: +49 (0)631 4161 290. Germany. Email: info@gebr-pfeiffer. A number of more than 2200 coal mills sold speaks for itself: on the basis of the proven MPS mill technology, we have adequate systems for coal and petcoke grinding.
More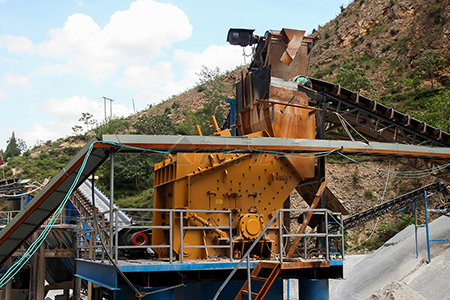
Ventilation Prediction for an Industrial Cement Raw Ball Mill by
the mill partitions, feed rate, the hardness of the feed material, and ball sizes in the mill compartments. Understanding the relationships between these variables from the grinding units can play an essential role in efficiently operating cement production lines [3–5]. One of the most critical variables in the cement ball mills is ventilation.
More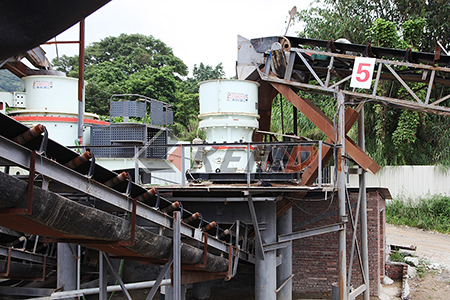
Use Cement Ball Mill Grinding Cement Clinker Cement Ball Mill
Cement Ball Mill. Feeding size: ≤25mm. Capacity: 1.5-105t/h. Functional advantages: Uniform abrasive, low energy consumption. Applications: Mainly used in cement plant, building materials, metallurgy, electric power and chemical industry, grinding all kinds of cement clinker and other materials. Email: info@ballmillssupplier.
More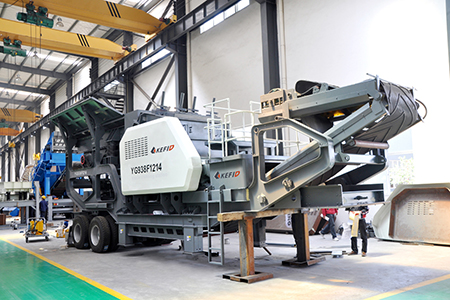
3 Necessary Cement Milling Comparison Ball Mill, Vertical Roller Mill
2020年11月5日 Vertical roller mill. Vertical roller mill, also called cement vertical mill, it grinds raw materials by the movement between grinding roller, millstone and grinding device. In general the grinding efficiency of vertical roller mill is 80% as much power as cement ball mill, reduce about 30% power consumption. vertical cement mill.
More- crusher mobile for sale
- broyeur a marteaux pour la production de ciment
- marteau de vitesse de concasseur
- Moulin à râper ultrafin en Mongolie
- sper balle broyeur de 50 tonnes par heure
- fabricant de concasseur à deux étages au Ghana
- broyeur à boulets de broyage krsher images de la machine
- double modèle rouleau crusher
- broyeur à béton et de lécran
- sable de concassage à hyderabad
- agrgat de pierre asiatique
- broyeur raffinage cacao
- concasseur situs sepatu concasseur surabaya à vendre
- co t de tpj miniusine de ciment usine de clinker
- Broyeur boulets de broyage de calcit