grinding plant raw mill in cement plant

Phone
+86 15538087991


Location
No. 201 Huaxiasanlu road, Pudong, Shanghai, China
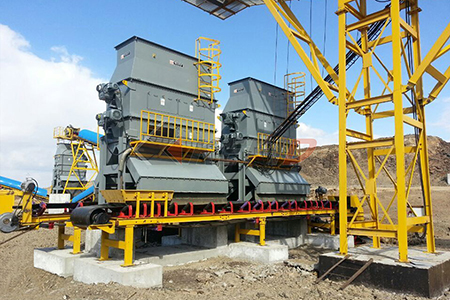
Rawmill - Wikipedia
Wet grinding is more efficient than dry grinding because water coats the newly formed surfaces of broken particles and prevents re-agglomeration. The process of blending and homogenizing the rawmix is also much easier when it is in slurry form. The disadvantage is that the water in the resultant slurry has to be removed subsequently, and this usually requires a lot of energy. While ene
More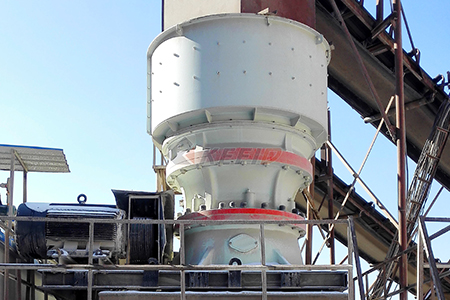
Raw Mill – Raw Mill In Cement Plant AGICO Cement Raw Mill
Raw Mill Selection Guide. Raw meal grinding is a vital link in the cement raw material preparation process. After the cement raw material is crushed, it will be sent into the
More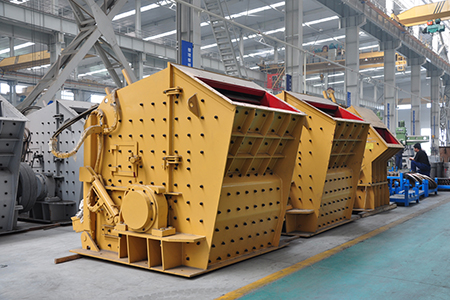
How does a raw mill work in a cement plant? - LinkedIn
2022年12月19日 A raw mill is a key piece of equipment used in a cement plant to grind raw materials into a fine powder. It works by crushing and grinding materials such as
More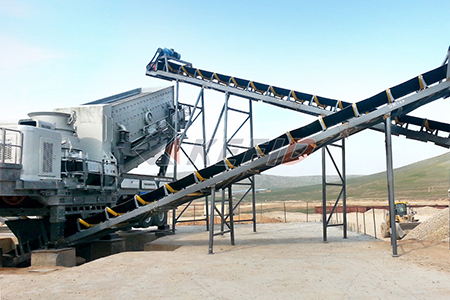
Reducing energy consumption of a raw mill in cement
2012年6月1日 The raw mill considered in this study is located in a cement plant located in Sanliurfa, Turkey. The plant is a single chamber mill with mechanical circulation system
More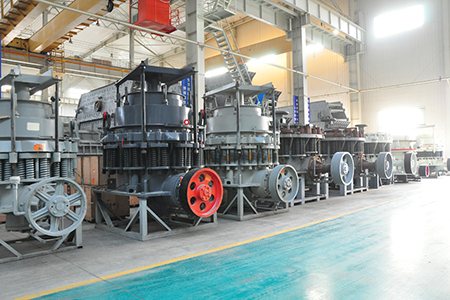
What does a Raw Mill do in Cement Plant? - ball mills supplier
How Does a Raw Mill Work in a Cement Plant? Grinding Plate. The grinding plate is the heart of a raw mill. It is a large, rotating steel plate with multiple layers... Grinding Rollers.
More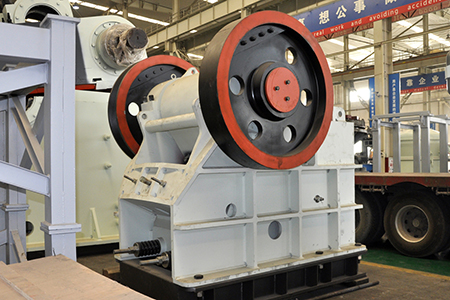
Review on vertical roller mill in cement industry its
2021年1月1日 For the past three decades the vertical roller mill has emerged to be the preferred choice for grinding raw materials. With the grinding capacity of a vertical
More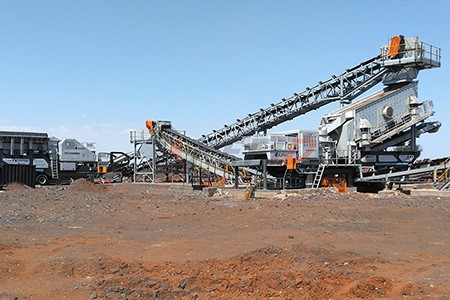
Raw Material Drying-Grinding - Cement Plant Optimization
Process: Dry Closed circuit dry-grinding. Type of mill: Ball and tube mills. Vertical Roller Mills (VRM). Horizontal roller mill (Roll Press) Roller press with Ball mill. Ball Mill Ball
More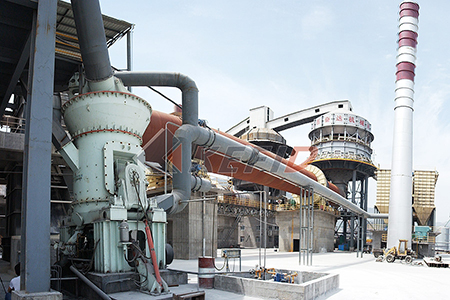
Modeling of energy consumption factors for an industrial cement ...
2022年5月9日 The plant has two cement production lines which in total produces 5300 t/day cement. The raw materials (lime, silica, and iron ore) enter the circuit through two
More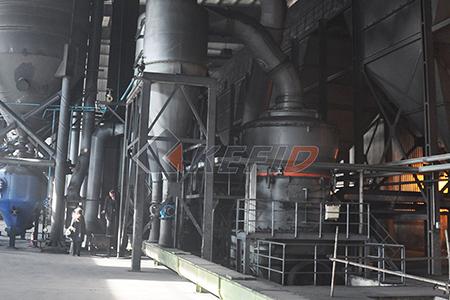
Energy-Efficient Technologies in Cement Grinding
2016年10月5日 In this chapter an introduction of widely applied energy-efficient grinding technologies in cement grinding and description of the operating principles of the related equipments and comparisons over
More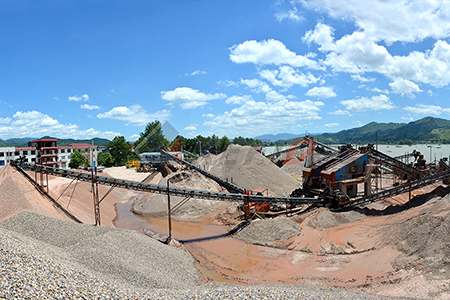
Cement Mill - Cement Grinding Machine - Cement
Raw mill is the grinding equipment applied in the raw material preparation process. In the wet process of cement production, raw materials should be ground into raw slurry with a water content of 30% – 40%. While in the
More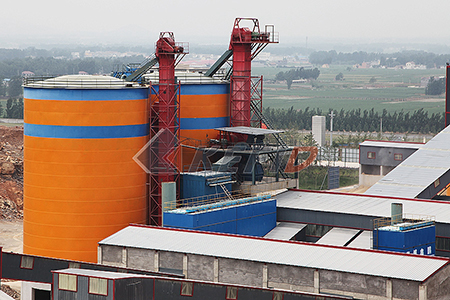
What does a Raw Mill do in Cement Plant? - ball mills supplier
Raw mills play a critical role in cement manufacturing. Here are some benefits of using a raw mill in a cement plant: Consistent raw mix quality: Raw mills produce a consistent and homogenous raw mix, which ensures consistent cement quality. Lower energy consumption: Raw mills use less energy compared to traditional ball mills, which makes
More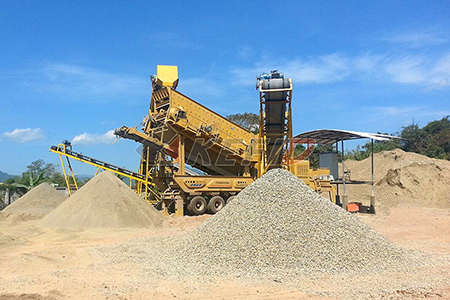
Cement Raw Mill in Cement Plant for Cement Raw Meal Grinding
Raw mill is mainly used for grinding cement raw meal in the cement factory production process. It is also suitable for metallurgical, chemical, electric power and other industrial mining enterprises to grind various ores and other grindable materials. Cement raw meal is a mixture of various raw materials before cement calcination.
More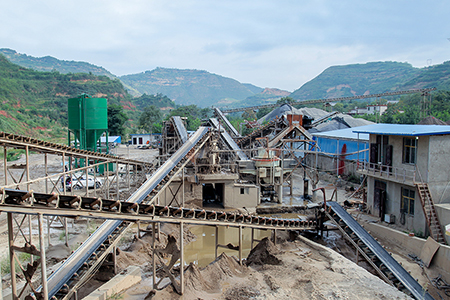
Vertical Cement Mill, Vertical Roller Mill Buy Cement Mill From
The vertical cement mill is large-scale cement grinding machine. With advantages of energy-efficient and stable quality, vertical roller mill is widely applied to many industries, such as cement, power, metallurgy, chemical and nonmetallic mining industry and etc. As a typical type of Cement Mill, vertical cement mill set crushing, drying, grinding, grading
More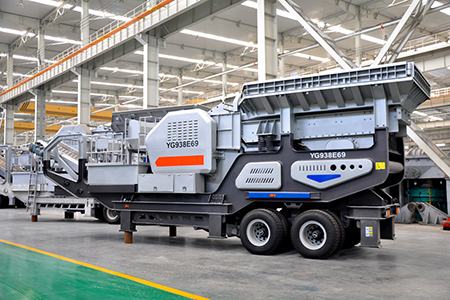
Coal Mill In Cement Plant, Air-swept Coal Mill Coal Mill
Feeding Size: <25mm. get price! Air-swept coal mill is the main equipment of cement plant, also called coal mill in cement plant, used for grinding and drying various hardness of coal, crushing the coal briquette into pulverized coal. It is the important auxiliary equipment of pulverized coal furnace. The air-swept coal mill runs reliably ...
More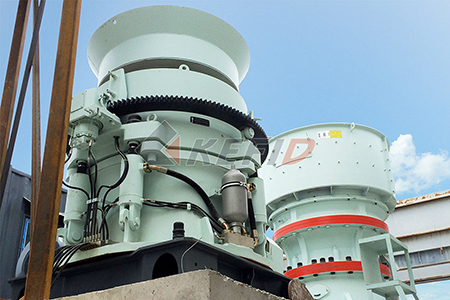
Review on vertical roller mill in cement industry its
2021年1月1日 Now a days Cement plants are producing 75–80% PPC 20–25% OPC due to high market demand of PPC. Production of PPC is cheaper and it's market rate is also lower than OPC by nearly 25 rupees per bag, so general consumer are attracted towards PPC cement. Cement companies also want to produce more and more PPC
More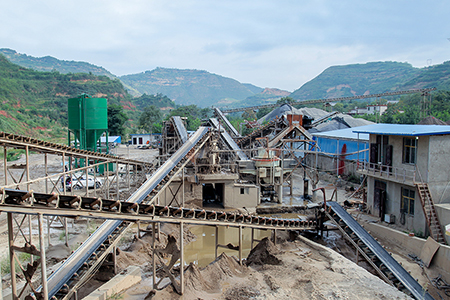
Cement Conveyor Belt Conveyor In Cement Plant AGICO
Cement conveyor refers to a belt conveyor in cement plant, which is necessary accessory equipment in the cement production line.. Belt conveyor is a kind of material handling equipment with strong adaptability, apply for conveying bulk density less than 1.67t / m³, it is mostly used for powder, granular, small lump materials and bagged materials, such as
More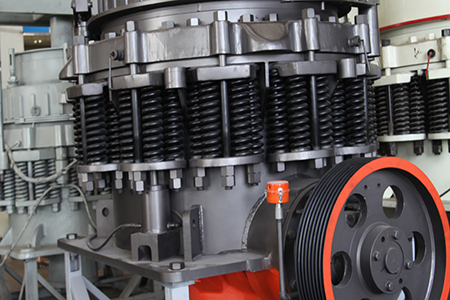
Modeling of energy consumption factors for an industrial cement ...
plant has two cement production lines which in total produces 5300 t/day cement. e raw materials (lime, silica, and iron ore) enter the circuit through two apron feeders. e raw materials are ...
More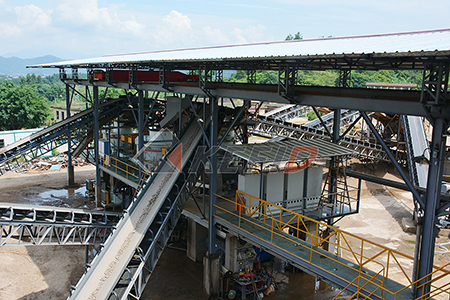
(PDF) MULTIPLE MATERIALS, ONE SOLUTION -ROLLER PRESS
2022年12月9日 Abstract. Up to two-thirds of the electrical energy in a cement works is consumed by grinding plants. Even more, when producing high fineness. By consuming the lowest specific energy per ton of ...
More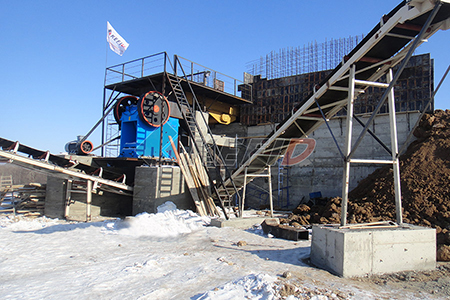
Cement Mill Cement Ball Mill Vertical Cement Mill AGICO
As a trusted cement plant manufacturer of China, AGICO Cement can provide high-quality cement mill and other kinds of cement equipment at competitive prices. Wide product range : For meeting various requirements from different clients, our cement mill range from cement ball mill, vertical cement mill, Raymond mill, coal mill in cement plant, etc.
More
Cement Industry Loesche
Cement Industry. LOESCHE Vertical Roller Mill: We do much more than rely solely on our unbeatable technology. Our designers are constantly coming up with new ideas and even more dependable components to
More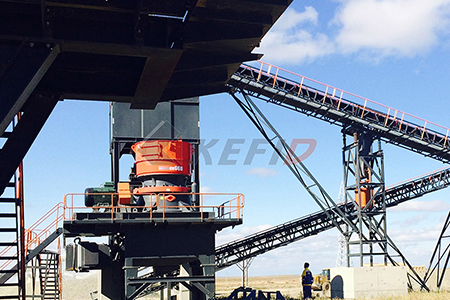
Mini Cement Plant EPC Cement Line Capacity 70 - 600 TPD
Mini Cement Plant Features. Cement plants with a clinker capacity below 700tpd can be called mini cement plants or small cement plants. Mini cement plants are very popular among small and medium-scale cement manufacturing enterprises since they do not require very large cement production capacities. Because of their small output capacities, the ...
More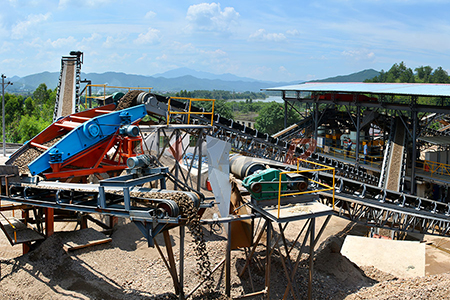
Mini Cement Plant, Small Cement Plant 50-1000TPH
Plant Capacity: 50 MT/Day. Plant Machinery: about 117155 dollars. Working Capital: about 103208 dollars. Total Capital Investment: about 348675 dollars. Return: 23.00%. Break Even: 63.00%. Start Your Mini
More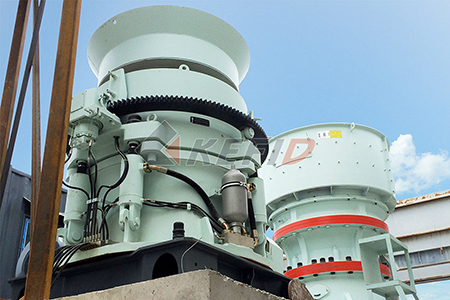
Review on vertical roller mill in cement industry its
2021年1月1日 Now a days Cement plants are producing 75–80% PPC 20–25% OPC due to high market demand of PPC. Production of PPC is cheaper and it's market rate is also lower than OPC by nearly 25 rupees per bag, so general consumer are attracted towards PPC cement. Cement companies also want to produce more and more PPC
More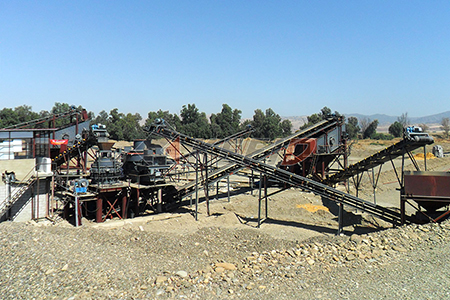
ball mill - thyssenkrupp Polysius
The proven classical option for cement grinding. Whether employed as a two-compartment separator mill in an independent grinding system, or in combination with a high pressure grinding roll, the Ball Mill is a robust and reliable alternative for cement and granulated blast furnace slag grinding.. Used in combination with the sepol® high-efficiency
More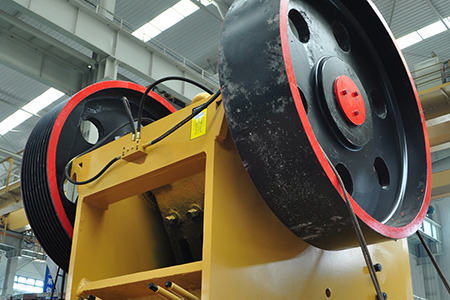
Performance Evaluation of Vertical Roller Mill in Cement Grinding
Keywords: Vertical roller mill, cement grinding, performance evaluation INTRODUCTION Cement production is highly energy consuming process with energy utilization of around 110-150 kWh/t (Villa, 2005).
More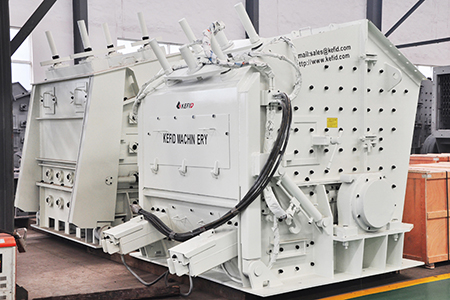
Coal Mill in Cement Plant
It is a mechanical device used to grind raw coal into pulverized coal powders. The most used coal mills in cement plants are air-swept ball mills and vertical roller mills. At present, most cement plants use coal as the main fuel in the clinker production process. The standard coal consumed by the new dry process for producing 1 ton of cement ...
More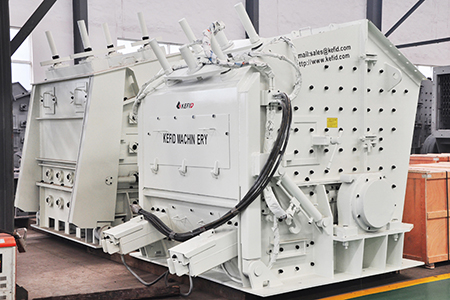
Reducing energy consumption of a raw mill in cement industry
2012年6月1日 About 2% of the electricity produced in the whole world is used during the grinding process of raw materials [1]. While total electrical energy consumption for cement production is about 100 kWh/ton of cement, roughly two thirds are used for particle size reduction [2]. About 65% of the total electrical energy used in a cement plant is utilized ...
More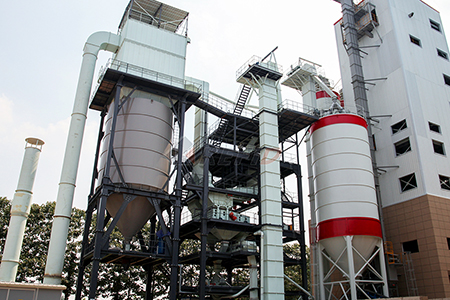
Pyroprocessing and Kiln Operation - Indian Cement Review
January 16, 2023. By. admin. Dr SB Hegde, Professor, Jain University, Bangalore, talks about pyroprocessing and the role of preheater, rotary kiln and clinker cooler in the cement manufacturing process. In the concluding part of the two-part series, we will learn more about the various factors aiding pyroprocessing. False Air in Pyro Processing.
More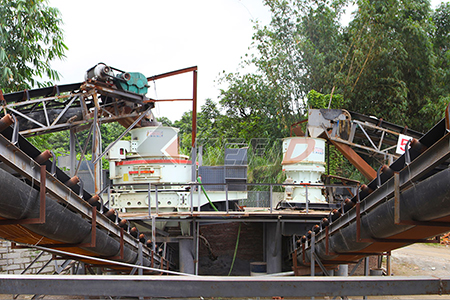
Cement Roller Press, Roller Press In Cement Plant HPGR Crusher
As new-type and energy-efficient cement grinding machine, cement roller press has advantages of energy-saving, high efficiency, less steel consumption and less noise. Both apply for new cement plant building and old cement plant revamping. According to the data, roller press helps ball mill system to increase the output by 30-50%.
More- machine de broyeur de pierres mobile le plus populaire
- concasseurs de pierre à vendre Haïti
- paroles de concasseurs à mâchoires shebang china
- matériaux utilisés pour broyeur vertical pulvériseur
- concasseur de pierres à mâchoires en phosphore
- concasseur biaya sewa bijih bes
- fabricant de dispositif d alimentation vibratoire en inde
- fabricants dusines de marteau
- ensemble des coûts de
- équipements de l'usine de traitement
- Convoyeur Pour L Extraction De Sable Et De Gravier
- el diseno de la planta trituradora de piedra nigeria
- roue montee petits concasseurs en inde
- force et force caracteristiques
- comment un rocher scène des uvres de concassage